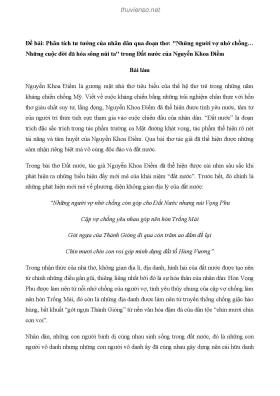
Preparaton of masterbatch containing anti-oxidation additive: effect of carrier resin ratio and additives content
Thông tin tài liệu:
Nội dung trích xuất từ tài liệu:
Preparaton of masterbatch containing anti-oxidation additive: effect of carrier resin ratio and additives contentVietnam Journal of Science and Technology 56 (2A) (2018) 56-62 PREPARATON OF MASTERBATCH CONTAINING ANTI-OXIDATION ADDITIVE: EFFECT OF CARRIER RESIN RATIO AND ADDITIVES CONTENT Duong Thi Thao1, Nguyen Phi Trung1, Hoang Thi Huong1, Tran Vu Thang2, Nguyen Van Khoi2, *, Trịnh Duc Cong2, Hoang Thi Phuong2 1 Institute of Research and Development on Novel Materials, 350 Lac Trung, Hai Ba Trung, Ha Noi 2 Institute of Chemistry, VAST,18 Hoang Quoc Viet, Cau Giay, Ha Noi * Email: khoinguyen56@gmail.com Received: 28 March 2018; Accepted for publication: 10 May 2018 ABSTRACT In this article, we investigated effect of carrier resin ratio and anti-oxidation additivescontent on properties of anti-oxidant additives Masterbatchs (MBs). The characteristics weremeasured by: melt flow index (MFI), morphology (SEM), tensile strength and elongation atbreak. The results indicated that: increasing LLDPE content in carrier resin led to decreasingmechanical properties, MFI weren’t uniform in MBs. With 80/20 of LDPE/LLDPE ratio, thetensile strength and elongation at break values were highest (21.0 MPa, 680.5 %). In addition,when increased anti-oxidant additives content, mechanical properties increased to upper limitvalue, then decreased. With 25 wt.% of anti-oxidant additives, the tensile strength andelongation at break values were highest (21.0 MPa, 654.7 %), MFI were uniform in MBs(12 g/10 m). SEM images were evidence of greatly distribution in sample containing 25 wt.%additives. Consequently, the 90/10 of LDPE/LLDPE ratio, 25 wt.% anti-oxidant additives wereselected to prepare MBs.Keywords: anti-oxidation master batch, carrier resin, LDPE, LLDPE. 1. INTRODUCTION Plastics industry has important role in our life. Plastics products has many advantages:flexible, good mechanical properties, good resistance to water, acid-base resistance, easy tomanufacture various products by different processing, such as: injection molding, extrusion,blow molding, etc. However, in processing and using of products, polymer materials areoxidized, leading to decreasing of performance. To solve this problem, anti-oxidation additivesare introduced into polymer matrix [1]. There were many literatures which reported about ability of anti-oxidation additives fordifferent polymer matrix. Jozef Rychlýa et al. [2] investigated UV resistance ability ofpolypropylene film incorporating with different additives: Irganox HP 136 and Irganox 1010.Preparaton of masterbatch containing anti-oxidation additive: effect of carrier resin ratio …Characteristics were performed by Fourier Transform Infrared (FT-IR) and carbonyl index. Theresults showed that Irganox 136 was more effective in anti-oxidation than Irganox 1010. M.J.Galotto et al. [3] studied on anti-oxidation of food packaging containing anti-oxidant additive(Irganox 1076) and evaluated the migration of additive. The experimental results indicated that,Irganox 1076 had good performance in anti-oxidation, there hadn’t migration and influence ofadditive to food. Hassanpour et al. [4] investigated mechanical properties, the changes inchemical structure, oxidation induction time (OIT) of HDPE/EVA blends containing thesynergist of Irganox 1010 and zinc stearate. The results showed that, anti-oxidation ability ofsamples containing anti-oxidant additive was better than the samples without additive. Manyliteratures reported that anti-oxidation additives performed effective even using low level ofcontent (0.1 - 0.5 wt.%). To distribute greatly additives in polymer matrix and decrease dust in processing, additiveparticles were introduced to polymer matrix by using masterbatch form (masterbatch is acompound of polymer matrix (as carrier resin) and one functional additive, which has lowcontent of polymer and high content of additive). Masterbatch has influence on mechanicalproperties and dispersion of additives in end-using product. Effective of masterbatch dependsstrongly on carrier resin and the content of additives. However, there weren’t many researcheson carrier resin and content of additives for masterbatch. So, the aim of this paper was toinvestigate the effect of carrier resin ratio and anti-oxidant additives content on properties ofmasterbatch samples. 2. EXPERIMENT2.1. Materials Low density polyethylene (LDPE) (density: 0.925 g/cm3, MFI = 4 (1900C/2.16 kgf)(supplied by LyondellBasell – Netherland), Linear low - density polyethylene (LLDPE)(density: 0.924 g/cm3, MFI = 21 g/10 min (1900C/2.16 kgf) (supplied by ExxonMobil – USA).Anti-oxidation additives: Irganox 1076 (AO1076), Irganox 168 (AO168), Irganox 1010(AO1010) were supplied by Tianjin Bestgain Science & Technology – China. Zinc stearate wasimported from Singapore. PPA 2800 was supplied by Thanh Loc Chemistry Company – VietNam.2.2. Methods.2.2.1. Anti-oxidation additive – containing masterbatch preparation Masterbatch samples were prepared containing the mixture of anti-oxidant agent (Irganox168/Irganox 1010: 67/33 in weight), carrier resin polyetylene (LDPE, LLDPE), zinc stearate,PPA2800 with calculated amount. Masterbatch samples were blended in Supermix machine forone hour to disperse the components. Well-mixed ingredients were melting mixed in twin-screwextruder (model: BP – 8177 – ZB), the temperature profile: 110-125-130-135-140-140 0C, at aconstant rotating speed of 24 rpm). The extrudate was cut in pellets with cylinder sha ...
Tìm kiếm theo từ khóa liên quan:
Vietnam Journal of Science and Technology Bài viết khoa học Tạp chí Khoa học Công nghệ Việt Nam Anti-oxidation master batch Carrier resinTài liệu có liên quan:
-
Việt Nam: Những khó khăn và kiến nghị cải thiện năng suất lao động trong bối cảnh hiện nay
3 trang 358 0 0 -
Giải pháp xây dựng TCVN và QCVN về xe điện hài hòa với tiêu chuẩn, quy chuẩn quốc tế
2 trang 151 0 0 -
3 trang 107 0 0
-
Phong cách lãnh đạo của đội ngũ lãnh đạo chủ chốt tại các doanh nghiệp nhà nước trong bối cảnh mới
4 trang 76 0 0 -
Định mức kinh tế - kỹ thuật đối với hoạt động thông tin khoa học và công nghệ
3 trang 44 0 0 -
Ứng dụng kỹ thuật hạt nhân giảm thiểu xói mòn đất
4 trang 41 0 0 -
Nhận diện một số nút thắt gây trì trệ trong đổi mới và phát triển khoa học và công nghệ
3 trang 38 1 0 -
Phân tích thông tin sáng chế trong lĩnh vực khai thác hải sản
3 trang 36 0 0 -
Hợp tác trong lĩnh vực y tế giữa Việt Nam và Angola
6 trang 34 0 0 -
Ninh Thuận: Nâng cao năng suất dựa trên nền tảng khoa học, công nghệ và đổi mới sáng tạo
3 trang 33 0 0 -
Green growth prediction of Ho Chi Minh city by the grey theory model
7 trang 30 0 0 -
Quyền sở hữu trí tuệ trong môi trường thương mại điện tử: Thực trạng và một số đề xuất
4 trang 29 0 0 -
4 trang 28 0 0
-
Kỹ năng viết và ngôn từ trong các loại bài viết khoa học bằng tiếng Anh
10 trang 27 0 0 -
Nghiên cứu chế tạo polyme blend kháng khuẩn từ nhựa nhiệt dẻo và polyguanidine
6 trang 26 0 0 -
5 trang 26 0 0
-
8 trang 26 0 0
-
7 trang 24 0 0
-
5 trang 24 0 0
-
Application of machine learning to fill in the missing monitoring data of air quality
7 trang 23 0 0